In today’s rapidly evolving industrial landscape, factories need more than just machinery to stay competitive. They require robust IT services that streamline operations, enhance productivity, and drive innovation. We’ve seen firsthand how the right technological infrastructure can transform manufacturing facilities from traditional production centers into smart, data-driven operations.
Our experience working with manufacturing clients has taught us that effective IT services for factories aren’t one-size-fits-all solutions. From network management and cybersecurity to IoT implementation and predictive maintenance systems, modern factories have unique technological needs that demand specialized expertise. As factories continue their digital transformation journey, partnering with IT service providers who understand both information technology and industrial operations becomes increasingly crucial.
Get in touch with our team to find out how we can assist with your IT needs
Reviews from our happy clients
Some of the businesses we have helped
Understanding IT Services for Modern Factories
IT services for factories as well as manufacturing companies are essential components that enable factories to digitally transform operations while ensuring quality, security, and seamless functionality across their enterprise systems. Modern factories rely on specialized IT solutions that address their unique operational challenges in today’s competitive industrial landscape.
Core IT Services for Manufacturing Facilities
Manufacturing IT services encompass several critical components designed to optimize factory operations. These services focus on:
- Equipment effectiveness optimization through advanced monitoring systems that increase return on assets
- Manufacturing process flexibility improvements via machine-to-machine integration and smart automation solutions
- Operational cost reduction through AI-based systems that identify inefficiencies and streamline workflows
- Regulatory compliance management for relevant manufacturing regulations
Comprehensive IT solutions for factories aren’t merely about implementing technology—they’re about strategic integration that aligns with specific manufacturing goals and challenges.
Benefits of Specialized IT Support
Manufacturing facilities gain significant advantages from tailored IT services that understand the unique demands of factory environments. These benefits include:
- Enhanced operational efficiency through systems that minimize downtime and maximize production output
- Data-driven decision making capabilities that transform raw operational data into actionable business intelligence
- Improved supply chain visibility with integrated systems that track materials and products throughout the production lifecycle
- Strengthened security posture that protects sensitive manufacturing intellectual property and operational technology
Key IT Challenges in Manufacturing Environments
Manufacturing environments face unique technological hurdles that can significantly impact productivity and profitability. These challenges require specialized IT solutions designed specifically for the manufacturing sector to ensure continuous operations, data security, and overall efficiency in production environments.
System Reliability and Downtime Prevention
System uptime is critical for manufacturing businesses where technology drives every aspect of production. Even brief disruptions can halt production lines, delay shipments, and directly impact the bottom line. Manufacturing operations depend on integrated IT services to maintain efficiency and competitive production levels, with any downtime translating into immediate revenue loss, decreased productivity, and weakened market position.
Key considerations for maintaining system reliability include:
- Proactive infrastructure management to identify and address potential issues before they cause disruptions
- Comprehensive monitoring systems that track equipment performance and network stability 24/7
- Redundant systems implementation to ensure operations continue during hardware failures
- Automated maintenance protocols that apply critical updates during scheduled downtime periods
- Disaster recovery planning with cloud-based backup solutions to restore operations quickly after unexpected events
Security Threats and Data Protection
Manufacturing companies face heightened cybersecurity risks as they store valuable intellectual property and operational data. Data breaches can compromise confidential information, damage operations, and tarnish reputation. Modern manufacturing facilities require robust security measures to protect against increasingly sophisticated cyber threats.
Effective security solutions for manufacturing environments include:
- Network security systems with firewalls, encryption, and access controls that safeguard sensitive data from unauthorized access
- SIEM (Security Information and Event Management) software that logs and analyzes activity across devices and network points using machine learning to detect suspicious events
- Vendor risk management protocols that assess and mitigate vulnerabilities within supply chain relationships
- Regular security audits to identify system weaknesses and implement appropriate countermeasures
- Comprehensive data protection strategies to prevent theft of proprietary manufacturing technology and intellectual property
These security measures work together to create multiple layers of protection, ensuring manufacturing data remains confidential while systems stay operational and protected from malware, hackers, and other cyberthreats that could compromise production integrity.
Essential IT Services for Factories
Manufacturing companies rely on specialized IT services to streamline operations, enhance productivity, and maintain competitive edge in today’s digital landscape. These services address the unique challenges of industrial environments while supporting digital transformation initiatives.
Network Infrastructure and Connectivity
Manufacturing facilities require robust network infrastructure to support mission-critical operations across production floors and administrative offices. A reliable network forms the foundation for all digital systems, from production equipment to inventory management. Key components include:
- High-availability networks engineered with redundant connections to eliminate single points of failure
- Industrial-grade Wi-Fi designed to function reliably in challenging environments with metal equipment, dust, and electromagnetic interference
- Segmented network architecture that isolates operational technology (OT) from information technology (IT) systems for enhanced security
- Low-latency connections supporting real-time monitoring and control systems across manufacturing operations
Manufacturing-specific connectivity solutions ensure production equipment, sensors, and control systems communicate efficiently, minimizing downtime and maximizing throughput across your facilities.
Cloud Solutions for Factories
Cloud services transform manufacturing operations by providing flexible, scalable access to computing resources and applications. These solutions deliver tangible benefits through:
- Cost reduction by shifting from capital-intensive on-premises infrastructure to scalable pay-as-you-go models
- Enhanced collaboration through real-time document sharing and communication tools that connect teams across multiple locations
- Remote access to critical data and applications for production managers, maintenance staff, and executives
- Advanced disaster recovery and backup solutions ensuring business continuity during system failures
Cloud technologies enable manufacturers to respond quickly to changing market conditions, scale resources during peak production periods, and implement advanced analytics without significant infrastructure investments. They also support compliance with industry-specific regulations through built-in security measures and certification frameworks.
IoT Integration and Smart Factory Technologies
Industry 4.0 technologies transform traditional factories into smart manufacturing environments through interconnected devices and data-driven optimization. Our comprehensive IoT integration services include:
- End-to-end automation of complex production workflows through sensor networks and control systems
- Real-time analytics enabling data-driven operational decisions and performance optimization
- Predictive maintenance systems that monitor equipment health and prevent costly downtime
- Smart inventory management solutions tracking materials and finished products throughout production cycles
These technologies create intelligent manufacturing ecosystems where machines communicate seamlessly, production data flows into actionable insights, and operations become increasingly efficient. By implementing IoT solutions tailored to your specific production requirements, you’ll gain unprecedented visibility into your manufacturing processes and unlock new opportunities for optimization.
At AGR Technology, we understand the unique IT challenges facing manufacturers today. Contact us to discover how our industry-specific expertise can transform your manufacturing operations with tailored technology solutions that drive productivity and growth.
Benefits of Managed IT Services for Factories
Managed IT services deliver tailored technological support that streamlines manufacturing operations while enhancing security and reliability. These specialized services help factories maintain continuous operations through proactive monitoring, maintenance, and rapid issue resolution.
Increased Operational Efficiency
Managed IT services boost operational efficiency by minimizing disruptive downtime and optimizing system performance. Remote monitoring tools identify potential issues before they impact production, while 24/7 support ensures immediate resolution when problems occur. Factory operations benefit from:
- Proactive maintenance schedules that prevent equipment failures during critical production periods
- Real-time analytics capabilities that provide actionable insights for process improvement
- Optimized workflows through integrated systems that eliminate redundant steps
- Enhanced production visibility with dashboard solutions that track performance metrics
By partnering with IT experts who understand manufacturing environments, factories maintain smooth operations even during peak production periods. Systems remain reliable and responsive, supporting consistent throughput and meeting delivery timelines.
Cost Reduction and Resource Optimization
Managed IT services transform unpredictable IT expenses into controlled, budgeted costs while maximizing resource utilization. Manufacturers gain significant financial advantages through:
- Predictable monthly expenses replacing unexpected repair costs and emergency service fees
- Reduced downtime costs with preventative approaches that maintain production continuity
- Optimized equipment lifespan through proper maintenance and timely updates
- Enhanced labor efficiency with automation tools that reduce manual data entry
Factory IT infrastructure operated under managed services typically experiences fewer failures and longer equipment lifespans. The combination of proactive maintenance, security management, and strategic technology planning delivers measurable ROI by preventing costly incidents and optimizing existing resources.
Implementing Industry 4.0 Technologies
Industry 4.0 conceptualizes the rapid integration of innovative technologies into manufacturing production and business processes. This digital transformation is spurred by the proliferation of big data, AI-driven analytics, edge computing, 5G, and IoT—promoting the shift from traditional factory models to smart manufacturing systems that significantly boost operational efficiency.
Automation and Digital Transformation
Automation and digital transformation form the cornerstone of Industry 4.0 implementation in modern factories. These technologies enable end-to-end automation of complex production workflows, transforming conventional manufacturing operations into smart, interconnected systems. Manufacturers adopting digital transformation experience:
- Streamlined workflows through automated processes that reduce manual intervention and human error
- Enhanced operational flexibility with systems that adapt to changing production requirements in real-time
- Improved product quality via consistent, precision-controlled manufacturing processes
- Reduced production costs by eliminating inefficiencies and optimizing resource utilization
AGR Technology can help manufacturing clients implement automation solutions that integrate seamlessly with existing systems. We design custom digital transformation roadmaps that align with your specific production goals, ensuring a smooth transition to Industry 4.0 capabilities without disrupting ongoing operations.
Data Analytics and Business Intelligence
Data analytics and business intelligence tools transform raw manufacturing data into actionable insights that drive strategic decision-making. These technologies enable:
- Real-time data-driven decisions based on comprehensive production metrics and KPIs
- Predictive asset maintenance that identifies potential equipment failures before they occur
- Intelligent troubleshooting capabilities that rapidly pinpoint and resolve production issues
- Analytics-based product customization that meets changing market demands
At AGR Technology, we build powerful data analytics solutions tailored to your factory’s unique operations. Our business intelligence platforms integrate with production systems to deliver real-time dashboards and reports that highlight optimization opportunities across your manufacturing processes.
Contact AGR Technology today to discover how our Industry 4.0 implementation services can transform your manufacturing operations. Our team of specialists will assess your current infrastructure and develop a strategic roadmap that leverages automation, data analytics, and smart factory technologies to drive sustainable growth and competitive advantage in today’s digital manufacturing landscape.
Selecting the Right IT Service Provider for Manufacturing
Choosing an IT service provider for your manufacturing facility requires careful consideration of industry-specific expertise and service capabilities. The right partner delivers tailored solutions that address your unique operational challenges while supporting digital transformation initiatives and maintaining regulatory compliance.
Industry Expertise Requirements
IT providers serving manufacturing environments need specialized knowledge beyond general IT competencies. Effective service providers demonstrate expertise in industrial control systems, operational technology (OT), and manufacturing execution systems (MES). They understand critical manufacturing processes like inventory management, supply chain logistics, and production workflows.
Look for providers with experience implementing solutions specific to manufacturing, such as:
- Equipment effectiveness optimization tools that increase return on assets
- M2M integration systems that improve manufacturing flexibility
- AI-based optimization solutions that reduce operational costs
- Compliance management systems
Service Level Agreements for Factory Operations
Manufacturing-specific Service Level Agreements (SLAs) differ significantly from standard IT contracts due to the mission-critical nature of factory operations. Effective manufacturing SLAs include:
- Response time guarantees based on issue severity and impact on production
- Recovery time objectives (RTOs) aligned with production schedules
- Uptime commitments for critical systems like MES, SCADA, and ERP
- Clear escalation procedures for emergency situations
- Provisions for preventive maintenance during planned downtime
- Metrics for measuring service quality and operational impact
The SLA should address 24/7 support options for facilities running continuous operations and include provisions for on-site emergency response when remote troubleshooting isn’t sufficient. Maintenance windows must align with production schedules to minimize disruption.
Negotiate SLAs that specify penalties for missed performance targets and include regular service reviews to monitor compliance. The most effective agreements establish a partnership approach where the IT provider shares responsibility for maintaining operational continuity and contributing to production efficiency goals.
When selecting an IT service provider, evaluate their willingness to customize SLAs to your specific manufacturing environment rather than offering one-size-fits-all agreements. The right partner understands that in manufacturing, IT service disruptions directly impact production output and revenue.
Conclusion
Modern factories need specialized IT services to thrive in today’s competitive landscape. The right technology partner brings both technical expertise and manufacturing knowledge to implement solutions that drive productivity while protecting critical systems.
From robust network infrastructure to IoT integration and comprehensive cybersecurity measures the technology foundation of manufacturing operations demands specialized attention. Managed IT services transform these challenges into opportunities while controlling costs.
Get in touch with our team to find out how we can assist with your IT needs
Frequently Asked Questions
What role do IT services play in modern manufacturing?
IT services provide the technological backbone for modern factories, enabling digital transformation, operational efficiency, and competitive advantage. They encompass network management, cybersecurity, IoT implementation, and predictive maintenance solutions specifically tailored to manufacturing environments. Effective IT infrastructure supports everything from production automation to supply chain management, making it essential for factories looking to thrive in today’s technology-driven industrial landscape.
How do specialized IT services benefit manufacturing facilities?
Specialized IT services deliver improved operational efficiency, data-driven decision-making capabilities, enhanced supply chain visibility, and strengthened security posture. They optimize equipment effectiveness, increase manufacturing process flexibility, reduce operational costs through AI implementation, and ensure regulatory compliance. Unlike generic IT solutions, manufacturing-focused services address the unique challenges of industrial environments, including 24/7 operations and mission-critical equipment requirements.
What are the key components of robust network infrastructure for factories?
Manufacturing facilities require high-availability networks, industrial-grade Wi-Fi solutions, segmented network architecture, and low-latency connections. This infrastructure supports mission-critical operations while maintaining security and reliability across factory floors. Properly designed networks accommodate industrial IoT devices, automation systems, and production equipment while protecting sensitive operational technology from cyber threats.
How are cloud solutions transforming manufacturing operations?
Cloud solutions provide manufacturers with flexible access to computing resources, enhanced collaboration capabilities, and robust disaster recovery options. They enable real-time data access across facilities, support remote monitoring and management, reduce capital expenditures, and facilitate easier scaling of IT resources based on demand. Cloud platforms also serve as the foundation for advanced analytics and AI implementations that drive manufacturing intelligence.
What benefits do IoT and smart factory technologies offer manufacturers?
IoT and smart factory technologies enable end-to-end automation, real-time analytics, predictive maintenance, and intelligent inventory management. These innovations provide unprecedented visibility into manufacturing processes, allowing for proactive issue resolution and continuous optimization. By connecting machines, systems, and products, IoT creates digital threads throughout operations that drive efficiency, quality improvements, and cost reductions.
How do managed IT services help maintain continuous factory operations?
Managed IT services provide proactive monitoring, regular maintenance, and rapid issue resolution that minimize unplanned downtime. They implement redundant systems, automated maintenance protocols, and comprehensive disaster recovery planning to ensure manufacturing systems remain operational. By shifting from reactive to proactive IT management, factories can address potential problems before they impact production, maintaining the continuous operations essential for manufacturing profitability.
What cybersecurity risks do manufacturing companies face?
Manufacturing companies face heightened cybersecurity risks including industrial espionage, ransomware attacks targeting production systems, and threats to intellectual property. The increasing connectivity between operational technology (OT) and information technology (IT) networks creates new vulnerabilities. Without robust security measures, manufacturers risk production disruptions, data breaches, safety incidents, and compliance violations that can have serious financial and reputational consequences.
How are data analytics transforming manufacturing decision-making?
Data analytics tools transform raw manufacturing data into actionable insights, enabling real-time decision-making, predictive maintenance, and intelligent troubleshooting. These solutions identify production bottlenecks, quality issues, and efficiency opportunities that would otherwise remain hidden. Manufacturers implementing advanced analytics report significant improvements in overall equipment effectiveness, product quality, and operational costs.
What should manufacturers look for in an IT service provider?
Manufacturers should select IT providers with industry-specific expertise in industrial control systems, operational technology, and manufacturing execution systems. The ideal partner understands both information technology and industrial operations, offers 24/7 support aligned with production schedules, and provides solutions tailored to manufacturing environments. They should demonstrate experience with similar manufacturing challenges and a track record of minimizing production disruptions during technology implementations.
Why are specialized Service Level Agreements (SLAs) important for manufacturing?
Manufacturing SLAs differ from standard IT contracts due to the critical nature of factory operations. Effective manufacturing SLAs include specific response time guarantees, recovery time objectives, uptime commitments, and provisions for preventive maintenance. These agreements should acknowledge the financial impact of production downtime and prioritize rapid resolution of issues affecting manufacturing operations, ensuring minimal disruption to production schedules and output.
Our Google Business profiles / Service areas:
Shepparton (HQ):
Melbourne service area:
Sydney service area:
Brisbane service area:
Goldcoast service area:
Related pages:
Industrial Machine Procurement Services
China Product & Machine Import Services
IT Services for engineering companies
IT Solutions for high-rise buildings
IT Solutions for commercial buildings
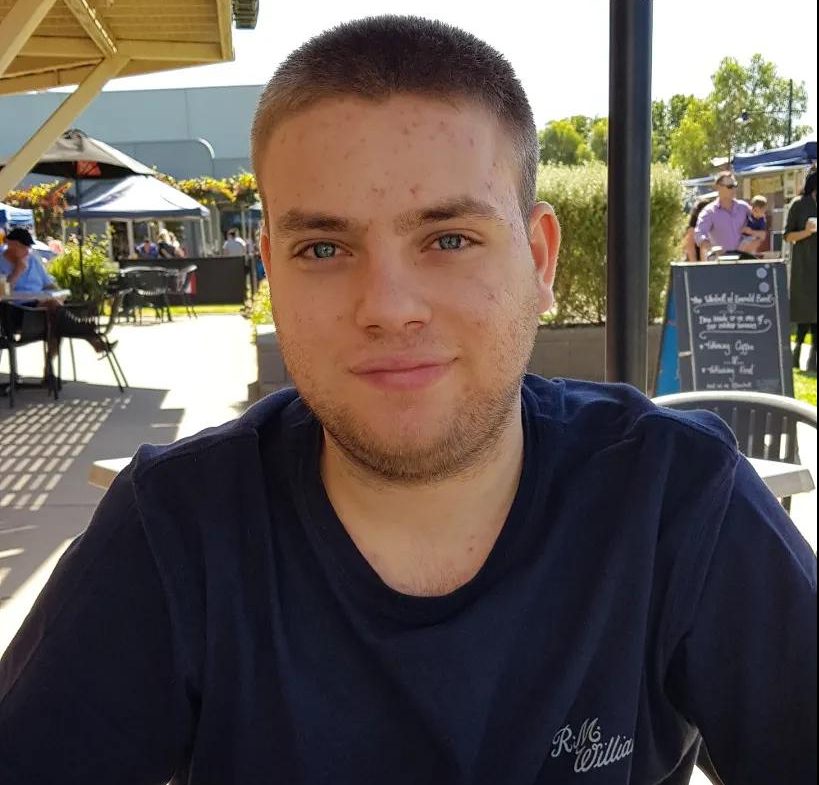
Alessio Rigoli is the founder of AGR Technology and got his start working in the IT space originally in Education and then in the private sector helping businesses in various industries. Alessio maintains the blog and is interested in a number of different topics emerging and current such as Digital marketing, Software development, Cryptocurrency/Blockchain, Cyber security, Linux and more.
Alessio Rigoli, AGR Technology